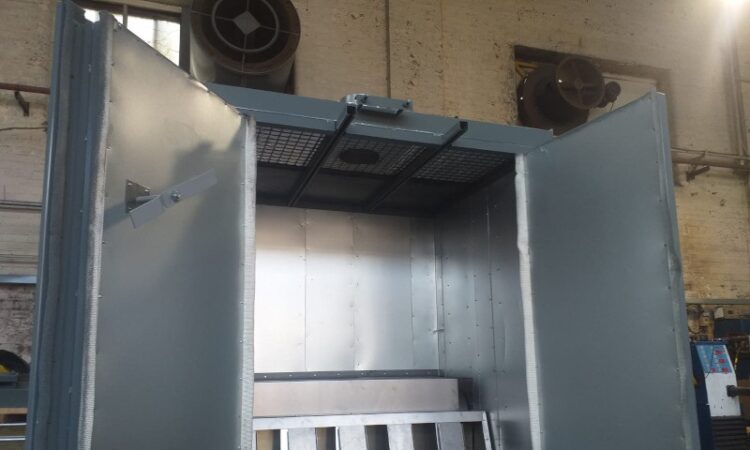
Expanding a manufacturing operation comes with challenges, but the right equipment can make a huge difference. Small manufacturers often need efficiency, reliability, and cost-effectiveness without sacrificing quality. An industrial curing oven designed for powder coating offers these benefits, making it a game-changer for businesses looking to improve production.
Lower Energy Consumption That Cuts Overhead Without Sacrificing Performance
Energy costs can drain profits, especially for small manufacturers trying to stay competitive. An industrial curing oven built for efficiency consumes less energy while maintaining high performance. Unlike older models that waste heat, modern ovens optimize energy use with advanced insulation and smart heating elements. This means manufacturers can reduce overhead costs without slowing down production or compromising coating quality.
Powder coating requires consistent temperatures to cure properly, and energy-efficient ovens deliver that without excessive power consumption. Many models are designed to retain heat longer, reducing the need for constant reheating. This results in lower operating costs over time while keeping output steady. For small businesses, saving on energy bills while maintaining a professional-grade finish makes industrial curing ovens a valuable investment.
The Advantage of Faster Curing Times for Quick Turnarounds
Time is money, especially in manufacturing, where production delays can disrupt schedules and hurt profits. An industrial curing oven with faster heat-up and curing times allows small manufacturers to complete jobs quicker. Unlike conventional drying methods, powder coating ovens rapidly reach the necessary temperature, ensuring a smooth, even finish in significantly less time.
Faster curing times mean businesses can take on more jobs without compromising quality. Instead of waiting hours for coatings to dry, manufacturers can move projects through the finishing process quickly. This efficiency allows them to meet customer demands faster, maintain production schedules, and even increase output without hiring more staff or expanding their workspace.
Does a Customizable Oven Design Give Small Manufacturers a Competitive Edge?
Standard ovens may not always fit the specific needs of a small manufacturer. Customizable industrial curing ovens provide flexibility by allowing businesses to adjust features based on production requirements. From size variations to adjustable airflow, manufacturers can choose specifications that maximize efficiency while keeping costs under control.
Custom ovens also offer adaptability as businesses grow. A manufacturer producing small batches today may need higher capacity in the future. A tailored design ensures the equipment remains useful even as production scales up. This level of control helps smaller companies compete with larger manufacturers by delivering consistent, high-quality coatings without overspending on unnecessary features.
Consistent Coating Application That Reduces Waste and Rework
Achieving a flawless powder-coated finish requires precision. Industrial curing ovens maintain the perfect balance of heat and airflow to ensure coatings cure evenly. This consistency prevents common issues like under-curing or over-curing, which can lead to wasted materials and rework. For small manufacturers, reducing errors means saving both time and money.
When coatings cure correctly the first time, manufacturers can avoid costly touch-ups and reapplications. Inconsistent curing often results in weak adhesion or poor durability, leading to customer complaints and product returns. A reliable industrial curing oven eliminates these problems by providing uniform heat distribution, ensuring every part receives the same level of curing, regardless of its position in the oven.
Scalable Solutions That Grow with Production Needs Without Major Upgrades
Growth is the goal for any small manufacturer, but expanding production can be expensive. Investing in an industrial curing oven that supports scalability prevents costly replacements down the line. Many modern ovens are designed to accommodate increased output without requiring major modifications, allowing manufacturers to scale up without starting over with new equipment.
Modular oven designs offer expansion options, so businesses can increase capacity as demand grows. This flexibility makes it easier to handle larger projects without disrupting workflow. Small manufacturers can start with a basic setup and gradually enhance their curing system, ensuring long-term cost efficiency while keeping up with production demands.
Smart Heat Distribution Prevents Defects and Ensures Uniform Finishes
Temperature inconsistencies can ruin a powder-coated surface, leading to uneven textures, bubbling, or peeling. An industrial curing oven with smart heat distribution technology ensures every part of the coated item receives the same temperature exposure. This feature minimizes defects and guarantees a smooth, durable finish.
Advanced heat control systems prevent hot spots and cold zones, eliminating variations in coating thickness. This means fewer rejected parts and a more reliable end product. For small manufacturers, maintaining quality without the risk of defects translates to higher customer satisfaction and fewer wasted materials. A dependable curing process keeps production moving efficiently while maintaining the professional standards that customers expect.